L.B. Foster helps CMK to lengthen the load
- Sep 02, 2021
- Rail
LB Foster was tasked with the design, manufacture and installation of an overhead power and free conveyor system that would double CMK’s production capacity.
CMK was founded in 1974 and has gradually expanded over the years, moving to the Birmingham area 26 years ago. A continuous programme of investment has kept the business at the forefront of technology culminating in this 2009 project. Bruce Gardiner is CMK’s commercial director; he explains his reasons for selecting LB Foster for the contract:
Our shortlist included two companies, one from overseas and the other from the UK. We chose to work with the local business, LB Foster, because they offered a solution that not only fitted the bill, it also offered better value for money. Bruce Gardiner, Commercial Director, CMK
There are 45 people working at CMK’s 52,000 sq ft facility at Oldbury, west of Birmingham. Half of this large building is dedicated to warehousing the aluminium extrusions and the remainder houses the powder coating treatment plant. Aluminium extrusions are transported through the treatment plant on the innovative overhead power and free conveyor system from LB Foster. The new solution has 7.2m long flight bars, which enables CMK to coat aluminium extrusions up to that length, opening up a new range of work.
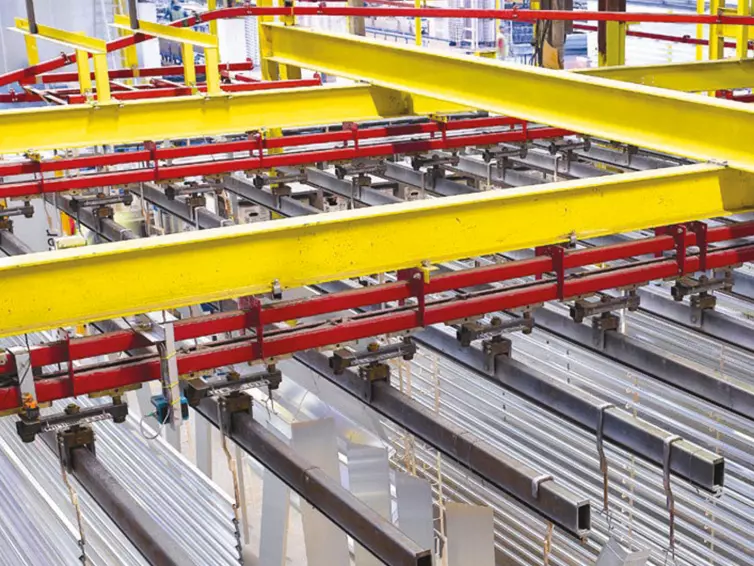
However, moving 7.2m long flight bars in the same orientation around a facility which incorporates structural columns poses its own set of problems. These were overcome with the use of powered cross transfers and now the loaded flight bars zigzag their way automatically around the different processes through pre-treatment, drying, powder coating, curing, cooling and finally packing.
The load capacity of the flight bars has more than doubled, from 200kg to 450kg, taking into account the fact that there is an increasing demand for heavier and stronger aluminium extrusions which are used as bombproof cladding for public buildings.
The conveyor system incorporates five separate drive units running between 1 and 6m per minute. The line which runs through the powder coating booth operates independently so that the conveyor speed can be altered to suit a particular job without changing the rate of the line going through the other processes.
LB Foster also provided the in-house designed control system for the conveyor. This system is operated by schematic touch screens; a feature which Bruce Gardiner feels is an added benefit to his company. He explains, “With the new controls software we can immediately see exactly what’s happening all around the plant and it is easy to alter production parameters.
“Our expansion strategy included rationalising our throughput from two powder coating lines to one, whilst still allowing us to change colour quickly, using up to 15 different colours a day. We also wanted to alter our pretreatment system from dip to spray to future proof the business against future legislation changes. This has helped to keep manual handling of the extrusions to a minimum; they are just loaded onto the flight bars at the start of the process and unloaded after cooling when they are ready for packing.
“We now have a fully integrated conveyor solution that has been specifically engineered to suit our particular requirements. It has enabled us to double our production output and transformed our facility into the UK’s most efficient powder coating line for multi-change finishes,” Gardiner concludes.